It can get confusing when we discuss “Peak” or “Obtainable” torque for small (fractional HP = less than 1HP/746W) gearmotors and motors because terminology and definitions sometimes change between AC and DC motors, gearmotors, or when a motor speed control is used.
AC Motors: in non-synchronous AC induction motors, we define obtainable torque as breakdown torque. Breakdown torque is the maximum torque a motor can produce, at rated voltage, without a relatively abrupt loss of speed. We define obtainable torque in synchronous motors as pullout torque. Pullout torque is the maximum torque the motor can produce at synchronous speed without pulling out of synchronism. These torque values are typically one and a half to two times the rated torque. Running at obtainable torque levels will in general cause an overheating problem, and must be limited to short time periods.
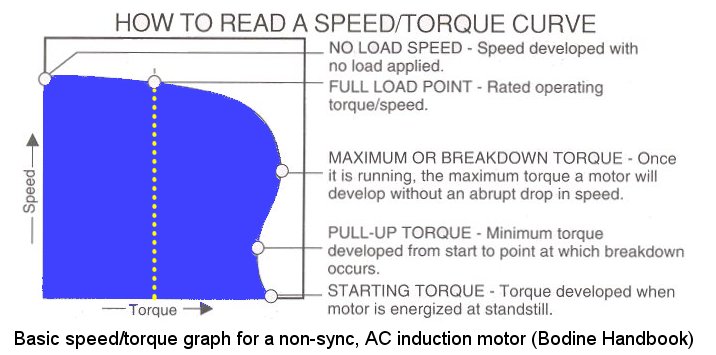
AC Motor Speed/Torque Curve (from the Bodine Handbook p7-25)
Permanent magnet DC (brush type) and brushless DC motors: can produce much higher peak or obtainable torque values than comparably sizes of AC induction motors. PMDC or BLDC motors, if not limited by a power supply, can produce peak/obtainable torques equal to their starting torques. These torques, depending on the motor design, could range from five to ten times rated torque. A more realistic definition of peak/obtainable torque in these types of motors is the maximum torque, which will not cause any permanent demagnetization of the motor’s magnets. Usually brushless motors are more susceptible to demagnetization than PMDC motors. The torque limits must be defined by the motor manufacturer and are dependent on magnet material and thickness, air gap size, amp-turns in the air gap and temperature. In either case running at these torque levels can only be tolerated for seconds or milliseconds as instantaneous extreme overheating — which can result in catastrophic failure. Motor circuit protection such as fusing should be considered as mandatory.
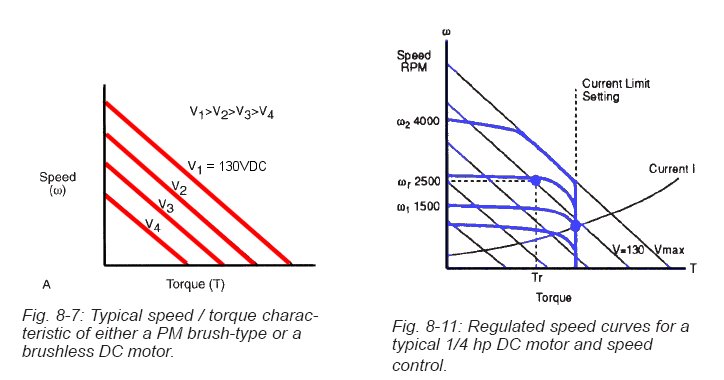
DC Motor Speed/Torque Curves (from the Bodine Handbook p8-8)
The torque ratings of gearmotors: are based on reducer design lives calculated to AGMA standards – and amongst other factors – they depend on gear type, lubricants, and bearing systems. When we discuss peak/obtainable torque in small gearmotors, we are referring to the torque value that will result in a reducer design life less than “continuous duty” life of the gearhead. We recommend to only operate small gearmotors at peak or obtainable torque on an “intermittent duty” basis. If a gearmotor is operated at these loads on a continuous duty basis, the gear train will eventually get damaged, and the gearmotor will likely not reach its rated design life (at rated torque and speed).
Electronic speed control systems: from Bodine Electric Company typically provide some type of circuit protection, current limiting or fusing. When used with our fractional horsepower (FHP) motors or gearmotors, their peak/obtainable torque is limited to whatever the maximum current is that the controller can supply without tripping the circuit protection device. In some cases the current limit is adjustable and can be set to protect the specific motor or gearmotor that is driven.
For more technical info on FHP Gearmotors, Motors, and Motor Speed Controls from Bodine Electric Company, visit our online “Tech Tools” section and download a free copy of the Bodine Handbook, and our recent Handbook updates.
Copyright © 10/2009 Bodine Electric Company. All rights reserved.